Understanding Titanium Bolts Manufacturers: Quality, Applications, and Innovations
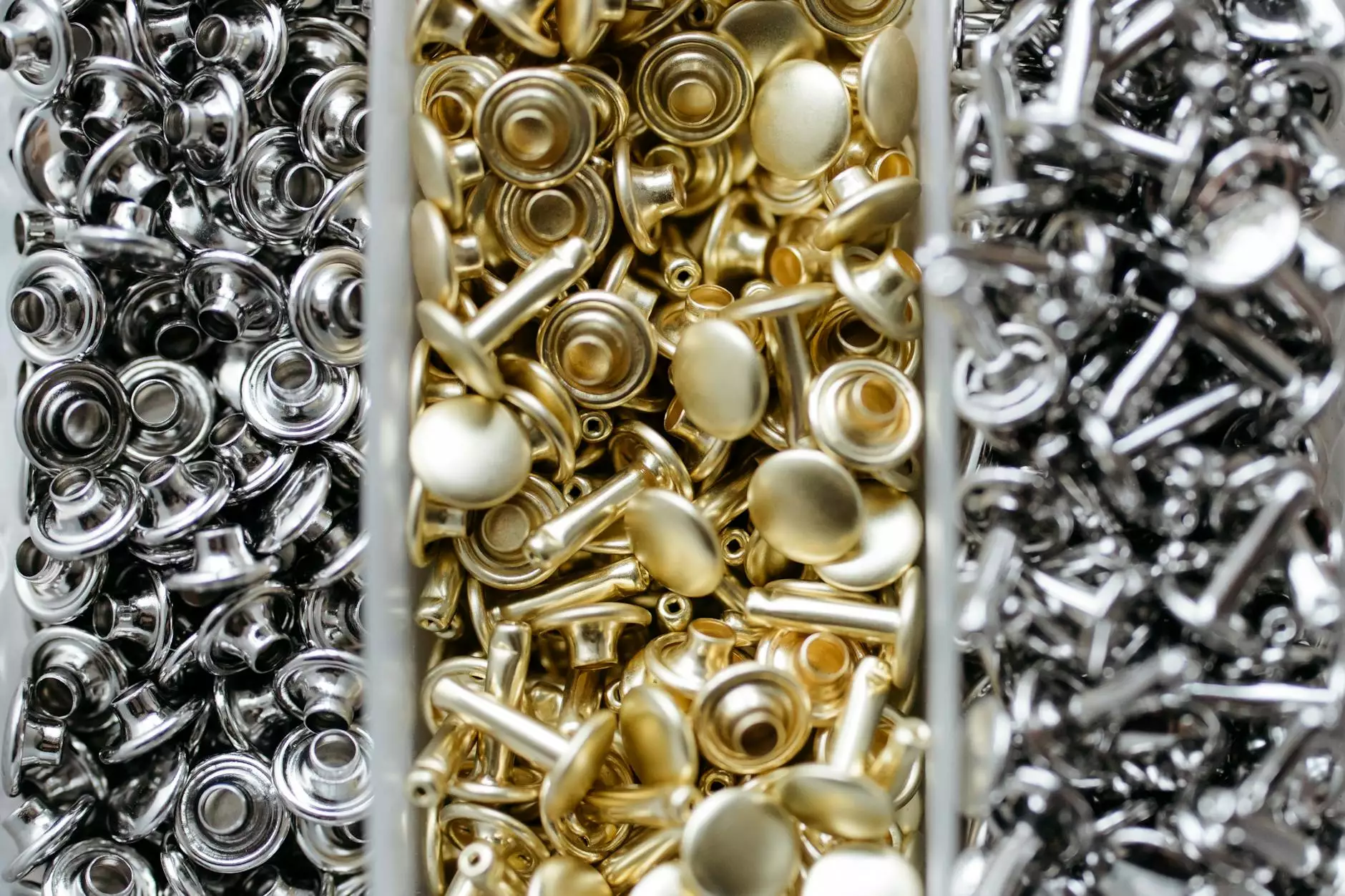
Titanium bolts play a critical role in numerous industries, providing strength, durability, and resistance against corrosion. When searching for reliable titanium bolts manufacturers, it's essential to understand what sets these manufacturers apart, the quality of their products, and the wide range of applications these titanium fasteners serve. In this comprehensive guide, we will explore the many benefits of titanium bolts, the manufacturing process, key applications, and tips on choosing the right manufacturer for your needs.
The Unique Properties of Titanium
Titanium is renowned for its unique properties, making it a superior material for fasteners. Some of its most notable characteristics include:
- High Strength-to-Weight Ratio: Titanium is incredibly strong yet lightweight, making it ideal for applications where weight savings are crucial.
- Corrosion Resistance: Titanium bolts resist corrosion when exposed to harsh environments, which prolongs their life cycle and reliability.
- High-Temperature Resistance: Titanium can withstand extreme temperatures, making it ideal for high-performance applications.
- Biocompatibility: Its non-toxic nature makes titanium bolts suitable for medical implants and devices.
Applications of Titanium Bolts
Due to their exceptional properties, titanium bolts are used across various industries. Notably, they excel in the following applications:
Aerospace Industry
The aerospace industry demands materials that are both lightweight and incredibly strong. Titanium bolts are extensively used in aircraft, spacecraft, and drones due to their ability to reduce overall weight while maintaining structural integrity. The use of titanium fasteners can lead to significant fuel savings and increased performance.
Automotive Industry
In the automotive sector, especially in high-performance and luxury vehicles, titanium bolts are favored for their strength and reduced weight. Manufacturers are increasingly using titanium fasteners to improve the performance of exhaust systems, suspension components, and engine assemblies.
Marine Applications
Given their remarkable resistance to corrosion from saltwater, titanium bolts are ideally suited for marine applications. They are commonly used in boat fixtures, underwater equipment, and brackish environments where traditional fasteners would typically fail.
Medical Industry
In the medical field, the biocompatibility of titanium is crucial. Titanium bolts are used in surgical implants, prosthetics, and dental applications, ensuring safety and longevity within the human body.
Industrial Manufacturing
Numerous industrial applications make use of titanium bolts for tooling, machinery, and assemblies. The robustness of titanium fasteners can significantly enhance the durability of equipment in demanding environments.
Choosing the Right Titanium Bolts Manufacturer
Finding the right manufacturer is vital for ensuring you receive high-quality titanium bolts. Here are some factors to consider when selecting a titanium bolts manufacturer:
1. Experience and Expertise
Look for manufacturers with substantial experience in the industry. An established company will have a proven track record and deep knowledge of titanium processing and fabrication.
2. Quality Assurance
Ensure the manufacturer adheres to strict quality assurance standards. Look for certifications such as ISO 9001 that demonstrate their commitment to quality control.
3. Production Capabilities
Assess the manufacturer's production capabilities, including their ability to handle custom orders and provide a variety of titanium fastener solutions to meet your specific needs.
4. Material Sourcing
Inquire about the sourcing of titanium materials. High-quality titanium sourced from reputable suppliers will influence the overall quality of the finished product.
5. Customer Service and Support
Evaluate the manufacturer’s customer service. Reliable support is essential for timely responses and solutions to any issues that may arise.
The Manufacturing Process of Titanium Bolts
The manufacturing of titanium bolts involves several intricate processes, each critical to producing high-quality fasteners:
1. Material Preparation
The process begins with selecting the right grade of titanium. The two most common grades used for fasteners are Grade 5 (Ti-6Al-4V) and Grade 2 titanium, each offering distinct advantages based on their intended application.
2. Forging
In the forging process, titanium bars are heated and shaped into rough bolt forms. This step enhances the material's structural integrity and improves its mechanical properties.
3. Machining
After forging, the blanks undergo precise machining to achieve the desired dimensions and surface finishes. CNC (Computer Numerical Control) machining is often employed for accuracy and efficiency.
4. Heat Treatment
A heat treatment process may be applied to alter the mechanical properties of titanium, increasing strength and durability while maintaining optimal performance characteristics.
5. Surface Finishing
Finally, the bolts undergo surface finishing processes such as polishing, anodizing, or coating to enhance corrosion resistance and aesthetic appeal.
Benefits of Using Titanium Bolts
Choosing titanium bolts offers numerous benefits that can positively impact various projects and applications:
1. Longevity
Due to their corrosion resistance and durability, titanium bolts boast longer life spans compared to traditional steel fasteners, saving time and money on replacements.
2. Weight Savings
Titanium's lightweight nature significantly reduces the overall weight of assemblies, leading to improved performance, fuel efficiency, and ease of installation.
3. Versatility
Titanium bolts can be tailored for a wide range of applications, from industrial sectors to aerospace, providing versatility unmatched by other materials.
4. Reduced Maintenance
The inherent properties of titanium decrease the need for extensive maintenance, allowing for easier management of equipment and systems.
Future Innovations in Titanium Bolt Manufacturing
The field of titanium manufacturing is continuously evolving, with advancements driving innovation and improvements in how titanium bolts are produced:
1. 3D Printing Technologies
3D printing is becoming increasingly significant in the manufacturing of titanium bolts. This technology allows for complex geometries, customization, and reductions in material waste.
2. Nano-coatings
Innovative nano-coating techniques are being developed to further enhance the properties of titanium bolts, improving wear resistance and corrosion protection.
3. Sustainability Efforts
As the demand for sustainable practices increases, titanium manufacturers are exploring eco-friendly sources and processes that minimize environmental impacts.
Conclusion
In summary, the world of titanium bolts manufacturers offers unparalleled benefits, innovative solutions, and diverse applications. Understanding the unique properties of titanium, the manufacturing process, and how to choose the right manufacturer will empower businesses to make informed decisions for their fastener needs. As industries continue to evolve and demand higher performance and sustainability, the role of titanium bolts will only become more critical.
By investing in high-quality titanium bolts from reputable manufacturers, companies can ensure longevity, performance, and a competitive edge in their respective markets. It's time to embrace the future – the future that includes the remarkable strength and versatility of titanium.