Unlocking the Potential of Screen Printing Silicone Inks
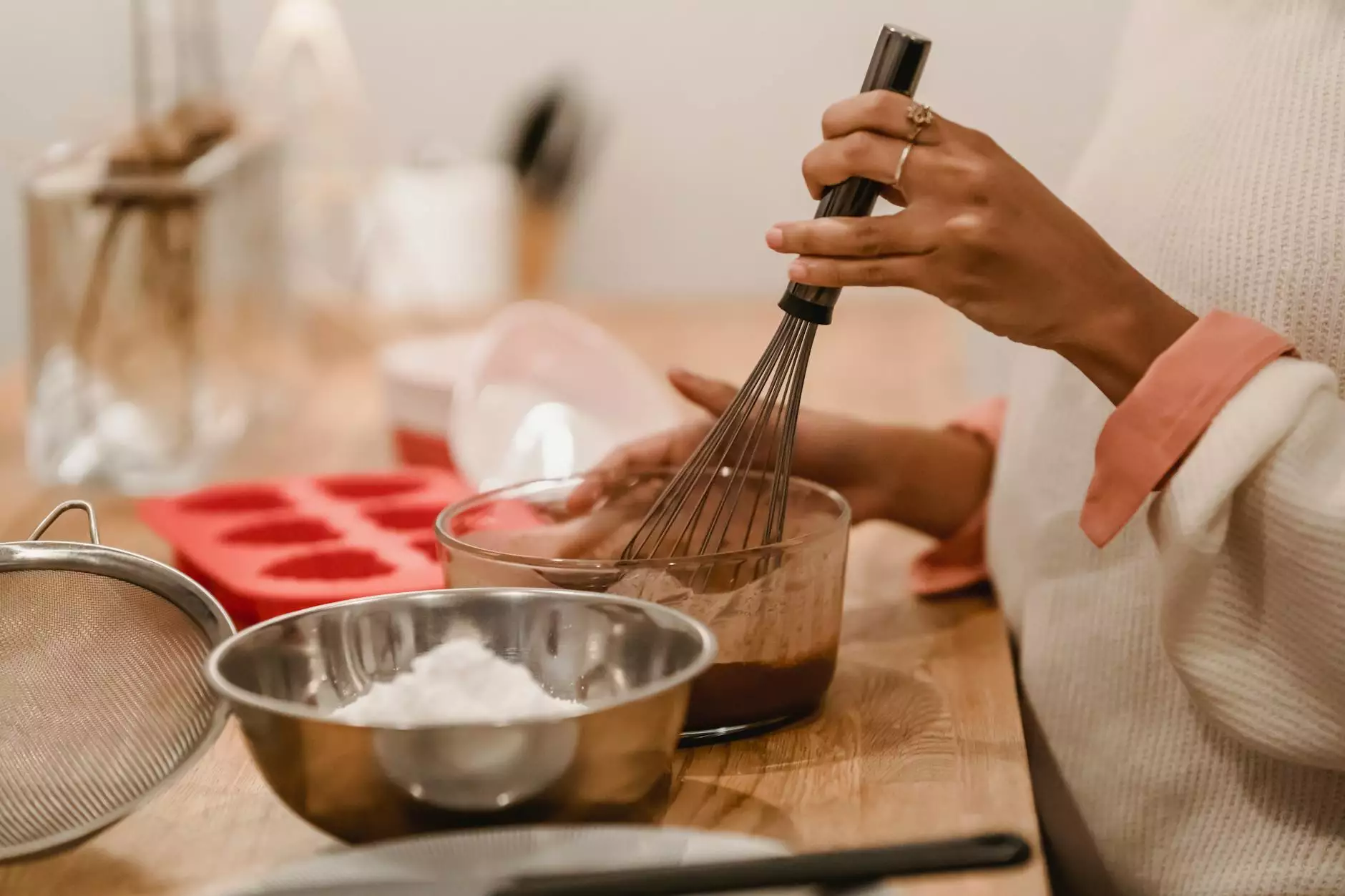
In the vibrant world of printing services, one particular innovation stands out for its versatility and excellence—screen printing silicone inks. Manufacturers and businesses are increasingly opting for silicone inks due to their unique properties that cater to demanding applications. In this article, we delve into the myriad benefits of silicone inks, their application processes, and why they are the future of printing technology.
The Rise of Silicone Inks in Screen Printing
The evolution of printing technologies has led to a surge of interest in silicone inks. Traditionally, solvent-based and plastisol inks have dominated the market; however, environmental concerns and consumer demand for high-quality, durable finishes have paved the way for a transition towards silicone inks.
Silicone inks are made from high-quality siloxane compounds, which provide unique qualities that enhance the experience of both printer and customer. Key reasons for their rising popularity include:
- Durability: Silicone inks are known for their exceptional resistance to abrasion, UV light, and extreme weather conditions.
- Flexibility: Unlike traditional inks, silicone inks maintain their integrity and flexibility after curing, making them ideal for fabrics and substrates that undergo stretching.
- Eco-Friendly: With a lower environmental impact, silicone inks are free from harmful chemicals, positioning them as a safer choice for both the environment and human health.
- Vibrancy: These inks produce bright, vibrant colors that last longer than traditional ink solutions.
Understanding the Process of Screen Printing with Silicone Inks
Screen printing is a multi-faceted process that involves several steps to achieve the desired result. The process of using screen printing silicone inks is not vastly different from traditional methods, but it does incorporate specific techniques suited for silicone. Here's how it works:
1. Preparing the Screen
The first stage involves preparing the screen with the desired design. A fine mesh screen is coated with a light-sensitive emulsion which hardens when exposed to light. The design is printed onto a transparent film, which is placed on the screen before exposure to light. After washing out the unexposed emulsion, a negative pattern of the design remains on the screen.
2. Mixing the Silicone Ink
Once the screen is ready, the silicone ink needs to be mixed properly. Silicone inks often come as a two-part system, comprising the base and a curing agent. It's essential to mix these components in the correct ratio to achieve optimal performance. Note: Always follow the manufacturer's guidelines when mixing to avoid any inconsistencies.
3. Printing the Design
With the ink prepared, the screen is aligned over the substrate—whether it’s fabric, plastic, or other surfaces. The printing process begins as a squeegee is used to push the silicone ink through the screen, depositing it on the material below. The design appears vividly, showcasing the high-quality properties of silicone inks.
4. Curing the Ink
The curing process is crucial. Silicone inks require heat to set properly. Depending on the specific ink and substrate, curing temperatures may vary, typically around 300°F. The curing ensures that the ink bonds strongly to the material, enhancing durability and flexibility.
Advantages of Using Screen Printing Silicone Inks
The benefits of incorporating silicone inks into a screen printing operation extend far beyond their fundamental qualities. Below are some of the key advantages:
- Enhanced Application Flexibility: Silicone inks can be utilized on diverse materials, including sportswear, promotional products, and outdoor textiles.
- Improved Wash Resistance: After curing, garments printed with silicone inks show remarkable wash durability, making them ideal for apparel that undergoes frequent washing.
- Customization: With various colors and finishes available, silicone inks allow for extensive customization options, catering to unique brand needs.
- Transparency and Color Mixing: Silicone inks can be transparent or opaque, providing options for layering and mixing colors to achieve distinct visual effects.
Applications of Silicone Inks in Screen Printing
The remarkable properties of screen printing silicone inks make them suitable for a myriad of applications:
1. Fashion and Sportswear
With a demand for vibrant, durable prints, the fashion industry benefits greatly from silicone inks. Not only do they withstand the rigors of repeated washings, but they also provide a soft hand feel, crucial for comfortable wear.
2. Promotional Items
Silicone inks are excellent for promotional products due to their long-lasting finish and resistance to fading. Items such as tote bags, customized t-shirts, and caps showcase impressive print quality that resonates with consumers.
3. Industrial Applications
In industrial settings, silicone inks fulfill roles where high durability is required. For example, printed labels and equipment graphics benefit from silicone's robustness and weather resistance, ensuring that the prints last for the lifetime of the product.
Choosing the Right Silicone Ink Supplier
When it comes to selecting a supplier for screen printing silicone inks, several factors should be considered:
- Quality: Ensure that the supplier offers high-quality silicone inks that meet industry standards.
- Support and Resources: A reliable supplier will provide technical support, including advice on mixing ratios, curing temperatures, and application methods.
- Range of Products: Look for suppliers that offer a comprehensive selection of colors and finishes to enhance your product offerings.
- Reputation: Research supplier reviews and customer testimonials to ensure you choose a reputable partner.
Conclusion: The Future of Screen Printing
As industries continue to evolve and place emphasis on sustainability and quality, screen printing silicone inks stand out as a remarkable solution poised to revolutionize the printing landscape. Their unique advantages make them an invaluable asset for any printing business aiming to provide exceptional quality and long-lasting results.
By embracing silicone inks, businesses not only cater to the present demands of the market but also prepare themselves for the future. From sportswear to promotional items, the potential applications are boundless, making it an opportune time to invest in this innovative technology.
In conclusion, Boston Industrial Solutions not only keeps pace with the innovative tide but positions itself to lead by offering superior printing services utilizing screen printing silicone inks. With the right tools and knowledge, printers can unlock limitless creative avenues and enhance their offerings significantly.